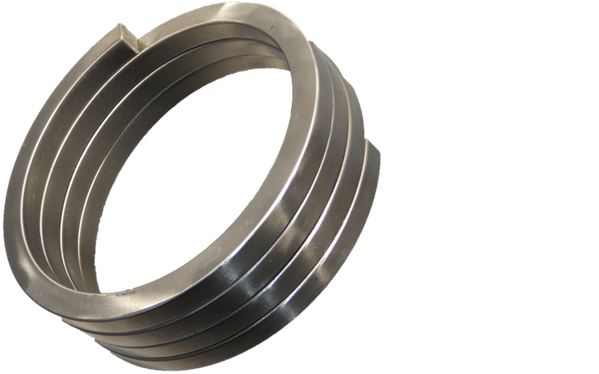
Advanced Magnet Lab is progressing with the development toward commercial manufacturing of its PM-Wire magnets, having received a new patent related to its “powder-in-tube” process for manufacturing them and, separately, forging an expanded business relationship with battery and rare-earth magnet recycler ReElement Technologies that involves an offtake agreement and financing.
According to the company, PM-Wire enables the manufacturing of both sintered and non-sintered permanent magnets at high volume, high yield, low cost and with better flexibility in shapes and magnetization direction as compared to conventional techniques. It can also enable the use of lower cost rare earth and non-rare earth materials, while improving the performance and lowering the cost of the end-use products such as motors.
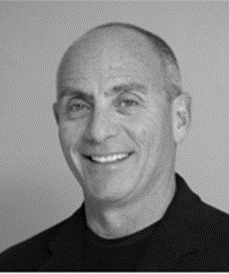
“We fill tubes with magnet alloy powders which are then reduced to the ideal packing density, cross-section and shape in a fully automated process,” explains Mark Senti, CEO of the Melbourne, Florida based company. “Magnet sizes can be very long, their shapes can be curved, rings or helical. Additionally, we have propriety tools and methods for magnetization, which provide an ideal magnetic flux distribution, including a continuously changing magnetization. Much like a Halbach array – but better. It is also very low cost to manufacture and super easy to assemble into a motor.”
Three patents related to PM-Wire have been issued and many more are pending, Senti reported to Magnetics Magazine in December. “One issued relates to the manufacturing process. Two of the patents are for dual-rotor motor wihich uses what we have invented. It is a single piece Halbach array where we have magnets that are manufactured to have a continuously changing magnetization. A perfect Halbach but in a ring or helix or straight. We have other enabling configurations including one that enables low critical rare earth and non-rare earth alloys. These compete with high grade alloys in motors.”
The company’s first step into high-rate commercial manufacturing will be non-sintered permanent magnets for select commercial and defense customers. AML has several development programs underway for enabling electric motor applications including a collaboration with Oak Ridge National Laboratory (ORNL) for an electric vehicle motor. AML plans to co-locate manufacturing with customers or supply chain partners, with preliminary discussions underway with several U.S. jurisdictions for site locations.
In the collaboration with ORNL, PM-Wire will be used to replace 2,750 complex Halbach array sintered magnets with eight non-sintered helical magnets and eliminate the need to actively cool the motor rotor with equal motor performance. AML envisions this demonstration as a potential springboard into commercial automotive applications.
Additionally, the company has several other active programs with commercial entities involving applications in industrial generators, aerospace, and defense. Going forward, AML plans to continue to expand its development programs and explore new material compositions for sintered and non-sintered magnets at its two locations in Florida, which can support an output of about 200 metric tons per year of permanent magnets. These locations, which encompass approximately 10,000 square feet, will continue to support customers with prototyping and research and development for alloys and magnets. The company foresees scaling manufacturing organically in 2024 through strategic partnerships with both customers and material providers.
Another example of how the technology can be applied, says Senti, is a magnet and motor topology which removes the North-South pole configuration and replaces it with a PM-Wire configuration which the company calls PM-Axial. Using the same magnet alloy, this solution provides Halbach array performance, increases operational temperature by 20%, eliminates iron in the rotor and reduces the rotor overwrap by 50%. More info is available in a previous article in Magnetics Magazine.
ReElement Antes Up, also Commits to Second Recycling Facility
The business deal came earlier when ReElement Technologies, a subsidiary of American Resources Corporation, executed a second rare earth oxide offtake agreement with AML to provide it high-purity raw rare earth elemental feedstock for its magnet production. Concurrently, the company made an initial strategic investment into AML to further advance the technology and commercialization. American Resources, based in Fishers, Indiana, led the investment round alongside a number of strategic investors and insiders in the form of a promissory note that can be converted into AML stock. The amount was not disclosed.
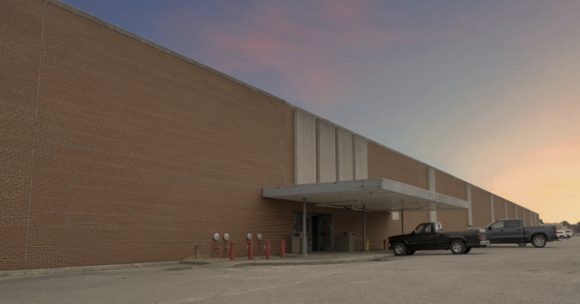
In mid-July, ReElement acquired controlling interest in the former RCA Thomson plant in Marion, Indiana, comprising 425,000 square feet manufacturing capacity on a 42-acre total campus for its rare earth and battery material refining. “After almost a year of careful analysis and extensive due diligence, we are excited to announce our expansion in Marion, Indiana for our second battery and rare earth element refining facility,” commented Mark Jensen, CEO of American Resources.
ReElement is planning for initial capacity of 2 metric tons per day of purified rare earth elements sourced from end-of-life magnets such as those found in high-efficiency motors, electric vehicles, wind turbines, power tools and computer hard drives. For battery materials, it is targeting initial capacity of 50 metric tons per day of lithium-ion battery input material sourced from end-of-life batteries and manufacturing waste.
For more info, see www.mitusmagnets.com, www.reelementtech.com, www.americanresourcescorp.com.