
PI (Physik Instrumente), a developer of diverse precision motion systems including magnetic levitation, piezo and other mechatronic technologies, has introduced a new series of motorized rotation stages using direct drive torque motors and ball bearings that extend its line of industrial rotary stages. Amidst a period of strong business growth, in other activities it is participating in a high-level group study that aims to integrate magnetic levitation into future nanoscale instrumentation, while also engaged in tripling the manufacturing capacity of a main production site in Germany, among several recent expansions.
The new family of direct-drive, ball bearing rotation stages are designed for demanding 24/7 applications that require high precision motion with eccentricity and flatness deviations below 1µm and along with high stiffness. Based on PI’s design and manufacturing expertise with ultra-high-precision air bearing rotary spindles, the new stages provide exceptional performance regarding travel accuracy, flatness and wobble. The ultra-precise deep groove ball bearings are preloaded and lubricated prior to delivery, making them maintenance-free. They can be mounted and operated in any orientation, horizontal, vertical, and hanging, a critical feature for many industrial automation applications.
For fast acceleration and a wide dynamic range, they are equipped with three-phase torque motors, transmitting torque directly and friction-free to the motion platform. Advantages of a direct-drive design over a worm-gear drive, says PI, are higher velocity and acceleration, faster response, as well as lack of backlash, friction, and wear in the drivetrain.
Absolute encoders supply explicit position information that enables the direct determination of each angular position, a great advantage over the traditional way of starting at a home position and continuous counting of encoder output increments. Therefore, position information is immediately available after power-up.
Key applications include optics and photonics, sample inspection, metrology, semiconductor testing, industrial automation, precision micro-assembly and biotechnology. The stages are designed to rotate objects such as machined parts and high precision optics, providing operators the ability to precisely control the angular position and orientation of their samples or equipment. The basic design of a direct-drive rotary spindle consists of a circular platform, driven by an integrated, non-contact torque motor. The platform is supported by a series of ball bearings. The secret to a smooth, uniform, and low-friction operation lies in the consistency of the balls and the precision of the raceways.
Pandemic fueled growth in PI’s innovation-driven markets
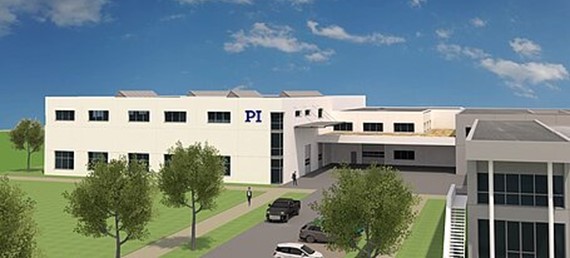
In fiscal year 2021, PI Group increased sales by 27 percent to more than $250M. Markus Spanner, CEO, is optimistic “We also expect two-digit growth rates over the next few years”. By the end of 2022, PI had invested more than $60M in the expansion of R&D and production capacities.
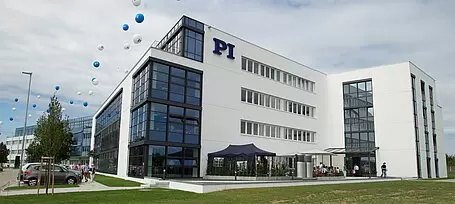
At the recent opening of its new 108,000 sq ft technology center at headquarters in Karlsruhe, company founder Dr. Karl Spanner commented, “We operate in a high-tech sector that has a profound effect on the future. There are no modern high-performance microchips being manufactured that PI is not involved in.”
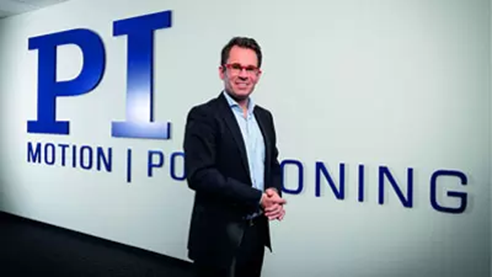
Magnetic levitation applications under active development
Magnetic levitation, often referred to as maglev, is a frictionless motion technology that uses magnetic fields to levitate and propel objects. It is used in various applications, best known from high-speed trains and magnetic bearings, and can have important benefit for precision motion control and nanopositioning.
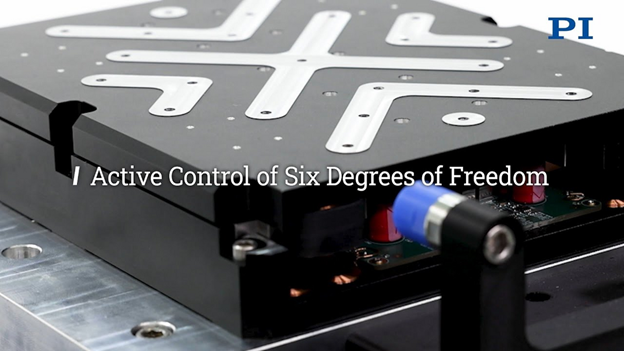
The basic principle of magnetic levitation is that like magnetic poles repel each other. To achieve magnetic levitation in its most simple form, two magnets are used; one magnet is placed in the object that needs to be levitated, and the other magnet is placed beneath it.
To make this principle useful for precision motion control, for example in linear stages, the magnets in the base must be electrically controllable coils and it takes more than just a pair to also control lateral motion, vertical motion and pitch, yaw, and roll, explains PI. In many practical implementations, Hallbach arrays are used to minimize the energy consumption, increase the load capacity, and reduce thermal energy dissipation.
A position sensing system is also required to provide feedback to the motion controller. Since no mechanical bearings restrict the motion of the linear stage platform to precisely one degree of freedom, a powerful, high-bandwidth multi-axis controller is required to keep all other degrees of freedom in check.
The benefits can be huge. Not being limited by a mechanical bearing adds an incredible amount of freedom to electronically correct bearing insufficiencies. It also allows for controlled small angular motions, such as to align a sample perfectly with an optics or camera or chip without the need for adding a bulky theta stage to the linear stage. In addition, vertical motions can be programmed, very useful for precise focusing.
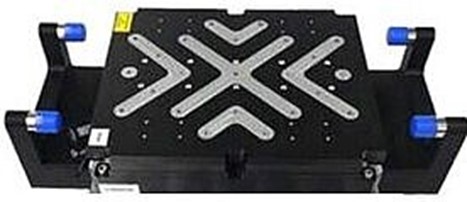
PI has been investing in research on magnetic levitation for nanopositioning applications and works with customers to move the technology forward with them. Technology demonstrators are available at its tech centers including the Silicon Valley center in California.
MetExSPM project explores MagLev suitability in nanometrology
One way in which PI’s capabability in magnetic levitation is being applied is through its participation in MetExSPM, a joint research project within the Euramet (European Association of National Metrology Institutes) organization that is investigating the traceability of localized functional properties of nanostructures with high speed scanning probe microscopy. The project could have significant impact on the future use of magnetic levitation for both industrial and research. The main goal is precision traceability for high-speed SPM leading to more reliable, cost efficient nanomanufacturing.
Today, complex nanostructures and nanodevices are used in photonics, quantum technology and nanoelectronics, and increasingly in healthcare and in novel materials research. Fast, accurate and traceable high-speed scanning probe microscopy (HSSPM) has great potential for use in identifying faulty nanoproducts across multistage production processes and offers the benefits of increased productivity and reduced wastage. Conventional scanning probe microscopy is either too slow to cover large sample areas or, if fast, can lack positioning accuracy. The project will develop essential scanning probe microscope components and ultimately a validated and traceable prototype HS-SPM measurement system suitable for use in industrial measurements.
Nanotechnology is expected to grow as its use in new applications increases across many diverse sectors, from consumer goods and healthcare to energy production. For example, the progressive miniaturization of advanced nanomanufacturing techniques which currently deliver nanodevices with feature sizes below 22 nm and complex nano-objects in the size range below 100 nm requires the introduction of fast, accurate and traceable measurement methods for the quality control of nanostructures and nanodevice dimensions and properties during production processes.
Industry, universities and research institutes perform many high-resolution measurements; however, says the research consortium, high resolution or high precision does not necessarily mean high accuracy. Without proper calibration and a good understanding of probe sample interactions, dimensional and property measurement errors may be as large as 30%. At present, in the nanomanufacturing, semiconductor, nanometrology and quantum technology fields, a lack of measurement traceability to the SI meter, the associated uncertainties, and the effects of speed on measurement accuracy do not meet user requirements for higher speed (>1 mm/s) combined with larger scanning area (>1 mm2) and better accuracy (~nm).
To turn high-speed SPMs from qualitative imaging instruments to high accuracy measurement instruments suitable for industrial quality control applications requires the development of scanning microscope stages with far greater stability, improved probing systems and advanced measurement strategies that combine high-speed scanning with the possibility to collect local electrical or mechanical properties.
The aim of the MetxSPM project is to enable the expansion of multi-functional probing microscopy, which is currently used for topography, to measurements of the localized functional electrical and mechanical properties of nanostructures and to produce guidance on the measurement methods needed to enable the demonstration of combined topography and electrical and/or mechanical properties as a starting point for future standardization.
The overall objective is to design and develop technologies for transforming HSSPM (~10 mm/s) metrology instruments for use in industrial high-speed quantitative multi-sensing metrology with a target traceable position measurement uncertainty of 1 nm. The developed instrument would be suitable for the industrial characterization of functional nanostructure property combinations including electrical, chemical, mechanical and dimensional.
One of the specific objectives of the project is to develop open-source experimental control and data processing software tools, for adaptive scanning and compressive sampling suitable for high speed SPM (~10 mm/s) surface nanometrology measurements over large areas (1 cm2), using hybrid stage combinations (piezoelectric and/or MagLev. This will enable real-time traceable quantitative multi-sensing measurements (topography combined with electrical or mechanical properties).
Accordingly, the MetxSPM project seeks to deliver a novel SPM scanner based on a hybrid combination of three stages: a 3-axes monocrystalline piezo stage, a 6-axes polycrystalline piezo stage and a 6-axes large-stroke magnetic levitation stage. The advantages of a maglev stage are its smooth and controllable accuracy and perfect cleanness during scan movements compared to conventional mechanically guided or air bearing systems.
Development of maglev stage a main challenge
Development of the maglev stage has been identified as the main challenge in the work package for a long stroke high-speed hybrid SPM scanner due to the requirements for high-quality sensor systems and complex control algorithms to achieve the necessary positioning performance and tracking accuracy. The project’s maglev stage will have multiple (at least 6 to 8) internal high-resolution positioning sensors, providing the advantages of compact size and low-cost. However, as the internal positioning sensors may have a limited accuracy for stage positioning, the project will also develop a high precision 6-DOF interferometric metrology system to further enhance the positioning accuracy (1 nm) of the scanner. This 6-DOF interferometric metrology system will also be used to characterize the positioning performance of the developed stages and has the additional potential for use as the direct positioning control of the maglev stage and/or piezo stages.
The PI Group employs more than 1,400 people worldwide in 15 subsidiaries with R&D, engineering and customer support centers on 3 continents. For more info, see www.physikinstrumente.com and www.ptb.de/empir2021/metexspm/home/.