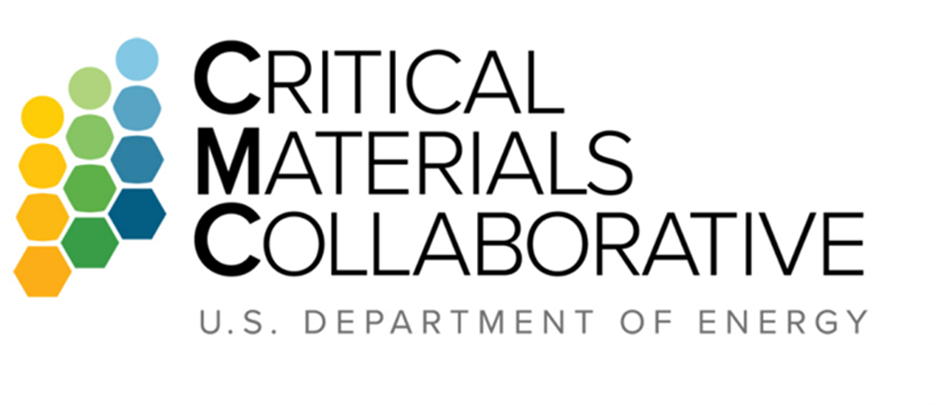
Developments in magnets and magnetic materials are prominent in $17 million of awards by the U.S. Department of Energy to boost domestic production and resources of critical materials. The new funding from the DOE’s Advanced Materials & Manufacturing Technologies Office and coordinated by its new Critical Materials Collaborative was announced December 10.
The 14 projects span an assortment of areas including rare earths recycling, hydrogen fuel cells, magnets for high-efficiency motors, high-performance lithium-ion batteries and high-yield low-defect power electronics but those involving magnetic technologies led the pack, topped by $2.7 million to Niron Magnetics.
Use of magnets with reduced critical materials content was a key sector:
- University of Texas at Arlington (Arlington, Texas): $1,000,000
- Ames National Laboratory (Ames, Iowa): $1,000,000
- ABB, Inc. (Cary, North Carolina): $1,520,000
- Niron Magnetics, Inc. (Minneapolis, Minnesota): $2,700,000
Recycling techniques and magnetic processing technologies are key aspects of several other awards.
University of Texas at Arlington
- Project: Pre-Pilot Production of High-Performance Magnets Based on the Cost-Effective Mountain Pass Mischmetal with Reduced Critical Materials Content
- Project Partners: MP Materials, Ames National Laboratory
- Location: Arlington, Texas
- Federal Funding: $1,000,000
The University of Texas at Arlington seeks to scale up production of a NdFeB magnet with partial substitution of neodymium and praseodymium with cerium and lanthanum, using a sintering aid. This project will not only reduce the use of critical REE in a permanent magnet by 30 to 40%, but it will also eliminate the need for dysprosium and achieve an increased energy product. By enabling the industry partner to scale the process for mass production, this project will ultimately accelerate the scale-up of domestic magnet manufacturing. The technology is based on LaCe-containing NdFeB magnets developed at the Critical Materials Innovation Hub.
ABB, Inc.
- Project: High-Efficiency Industrial Motors Using U.S.-Sourced Non-Rare-Earth Permanent Magnets from Mining Byproducts
- Project Partners: Powdermet Inc., Ames National Laboratory, North Carolina State University
- Location: Cary, North Carolina
- Federal Funding: $1,520,000
ABB aims to develop and prototype motors using manganese-bismuth (MnBi)-based polymer-bonded permanent magnet technology for general purpose and traction applications. If successful, this technology would eliminate the use of critical materials in industrial motors and non-drivetrain automotives, which account for 38% of the market combined and would lead to an opportunity for >10% market share adoption. The technology builds upon prior work funded by the government to develop a suitable non-REE magnetic material, which lowers the technical risk and improves efficiency and cost-effectiveness; and the motor topology selection is compatible with EV industry.
Niron Magnetics, Inc.
- Project: Variable Flux Field Intensifying Motors Using Iron Nitride Permanent Magnets
- Project Partners: Illinois Institute of Technology, Oak Ridge National Laboratory
- Location: Minneapolis, Minnesota
- Federal Funding: $2,699,810
Niron Magnetics, Inc. will design, analyze, and fabricate a prototype permanent magnet motor without the use of critical rare earth materials. This technology will utilize Niron’s variable flux field intensifying iron nitride permanent magnet material, with a potential for significant shift in the state-of-the-art for high-performance electric motors. If successful, the motors would demonstrate a 50% decrease in carbon dioxide as compared to a NdFeB-based motor and would increase the efficiency of the motor by 2% over the entire drive cycle.
Ames National Laboratory (1)
- Project: Mechanically Robust High Magnetic Performance NdFeB Magnets with Resilience in Applications and Reduced Magnet Wastes
- Project Partners: Noveon Magnetics Inc., University of Arizona
- Location: Ames, Iowa
- Federal Funding: $1,000,000
Ames National Laboratory and its partners will prototype and scale up the tough neodymium-iron-boron (NdFeB) magnet technology developed at the Critical Materials Innovation Hub (CMI Hub). The technology aims to improve manufacturing efficiency by enhancing the magnet’s mechanical toughness, which in turn reduces the failure rate when machining the blocks into parts, especially those with complex geometries. The technology has been successfully demonstrated at the bench scale (TRL 3) with mechanical and magnetic performance superior to the baseline commercial products and this project aims to accelerate it to pre-pilot scale (TRL 6). Improving the magnet’s strength, reducing waste production and machining failure rate, increasing the magnet’s service life, and making it easier to recycle the magnets will directly lead to savings in the critical materials required to make the traditional NdFeB sintered magnets. The technology was recognized with a 2021 R&D 100 Award. Two patent applications were submitted to the USPTO.
Virginia Polytechnic Institute & State University
- Project: Pilot Demonstration of the GAME Technology To Boost Critical Mineral Production
- Project Partners: Phinix LLC, Rio Tinto, University of Kentucky
- Location: Blacksburg, Virginia
- Federal Funding: $1,000,000
Virginia Polytechnic Institute and State University (Virginia Tech) intends to scale up its novel solvent extraction technology, which efficiently extracts metals of low concentrations using high aqueous to organic phase ratios. A prototype of the gas-assisted microbubble extraction (GAME) technology has been successfully fabricated and validated through benchtop batch testing. To achieve pilot scale success and move GAME’s technology readiness level to six, the project will utilize acid mine drainage generated from a copper mine, containing critical and valuable elements, most of which are present in low concentrations, as the primary feedstock. The project looks to produce critical materials with a minimum purity of 95% for neodymium, dysprosium, and yttrium, and 99.5% for nickel, cobalt, manganese, and copper.
Ames National Laboratory (2)
- Project: Critical Rare-Earths-Free Cerium Gap Magnets
- Project Partners: TdVib LLC, HL Mechatronnics, Purdue University
- Location: Ames, Iowa
- Federal Funding: $1,000,000
Ames National Laboratory seeks to demonstrate a cost-competitive, one-step castable, grain-oriented, and fully dense cerium-based gap magnet. The project will focus on optimization of directional solidification necessary to achieve the target performance of an energy product of 15 MGOe. The project will scale up the process to fabricate the cerium-based gap magnet to produce 1 to 5 kg of material. Through these project objectives the team will deliver a fully dense anisotropic gap magnet that aims to satisfy needs for a wide range of middle-energy applications including steeper and micro motors, motors for drones, and electric vehicles. The background work for this technology won a R&D 100 Award and is patented.
Oak Ridge National Laboratory
- Project: A Novel Energy-Efficiency Scalable Membrane Process for Separation and Recovery of Rare Earth and Domestic Sources
- Project Partner: North Carolina Agricultural and Technical State University
- Location: Oak Ridge, Tennessee
- Federal Funding: $1,000,000
Oak Ridge National Laboratory aims to develop an energy-efficient, cost-effective, high-yield and environmentally friendly integrated process for separation and recovery of high-purity rare earth elements (REEs) from domestic waste stream sources and mining tailings. This will be performed using a single-step integrated membrane solvent extraction process, based on the concept of using low-cost, robust membrane supports for solvent extraction. By reducing the number of stages involved in solvent extraction, this process offers a small overall footprint with linear scalability and can achieve high extraction rates of REEs from unconventional feedstocks while maintaining low energy and cost requirements. If successful, the project will demonstrate separation and recovery of REEs with >99.5% purity and >90% yield from domestic mine tailings and waste streams, as well as successful separation of heavy REEs from the resulting product of mixed REEs.
Texas Agricultural and Mechanical University
- Project: Recovery of Rare Earth Elements from e-Waste using Functionalized Mesoporous Carbon Foams
- Project Partner: Oak Ridge National Laboratory
- Location: College Station, Texas
- Federal Funding: $1,280,553
Texas A&M University plans to develop a cost-effective and sustainable solid-phase extraction (SPE) method for rare earth elements (REEs) recovery from electronic waste (e-waste). SPE using crumpled graphene-balls-based porous membranes will be developed for neodymium, praseodymium, and dysprosium recovery. The project seeks to develop a novel synthetic approach of tripodal diglycolamide ligands with stronger REE affinity using simple, cheap, readily available chemicals in just four steps for enhanced scalability. It will also design self-supporting tripodal mesoporous carbon foams as stable and reusable adsorbents for REE recovery without requiring frequent extractant replacement or cleaning and develop a low-cost and scalable SPE method that eliminates the use of organic solvents in the REE separation process.
Infinite Elements
- Project: Techno-Economic and Life Cycle Assessment of Biohydrometallurgical Critical Mineral Recovery from E-Waste and Manufacturing Scrap
- Project Partner: National Renewable Energy Laboratory
- Location: El Paso, Texas
- Federal Funding: $1,500,000
Infinite Elements aims to demonstrate a combination of bioleaching and advanced peptide design to efficiently recycle critical materials from electronic waste (e-waste). The project aims to increase critical material recovery yields from 45% to 85% while improving energy efficiency by more than 50%. The process includes three modules: dissolution, biofilter production, and refining. It is capable of handling diverse feedstocks of e-waste and can recover critical materials with an 80% reduction in emissions compared to conventional hydrometallurgy. If successful, the project would demonstrate a commercially viable project that could be used with a variety of waste streams to produce rare earth elements domestically.
The Critical Materials Collaborative is a new mode of connection created by DOE to improve and increase communication and coordination among DOE, government agencies and stakeholders working on critical materials projects. It was launched in 2023 and born out of the need for a critical materials convening arm. See www.energy.gov/cmm/critical-materials-collaborative.