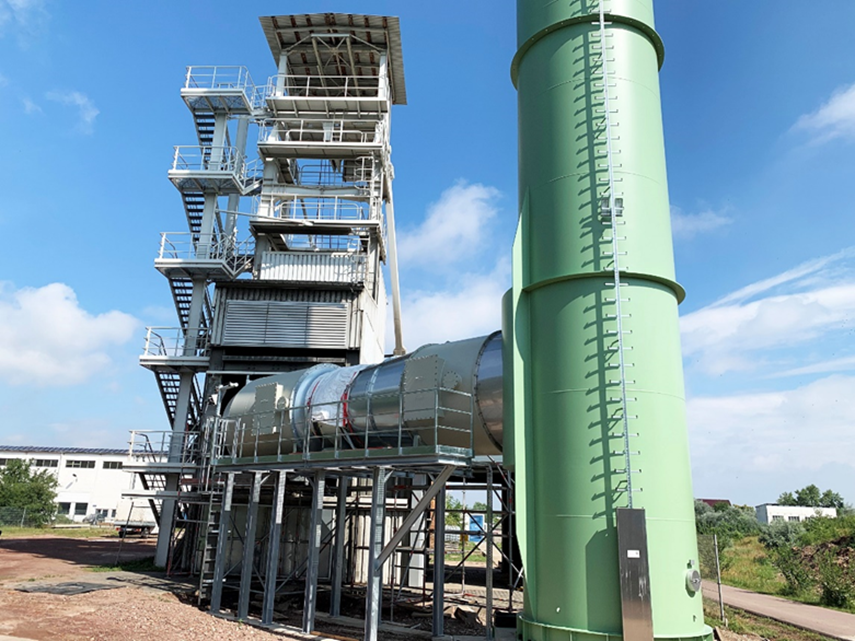
Novenco Building & Industry, a leading Danish manufacturer of ventilation fans and systems, called on Nidec Leroy-Somer to supply a powerful but energy efficient electrical motor for driving the largest fan in their ZerAx range of axial fans. The system was specially designed for extracting carbon dioxide from a German backfill mine and needed to emphasize climate neutrality. Now, one of Nidec’s new Dyneo+ eco-efficient permanent-magnet synchronous reluctance motors drives the giant fan.
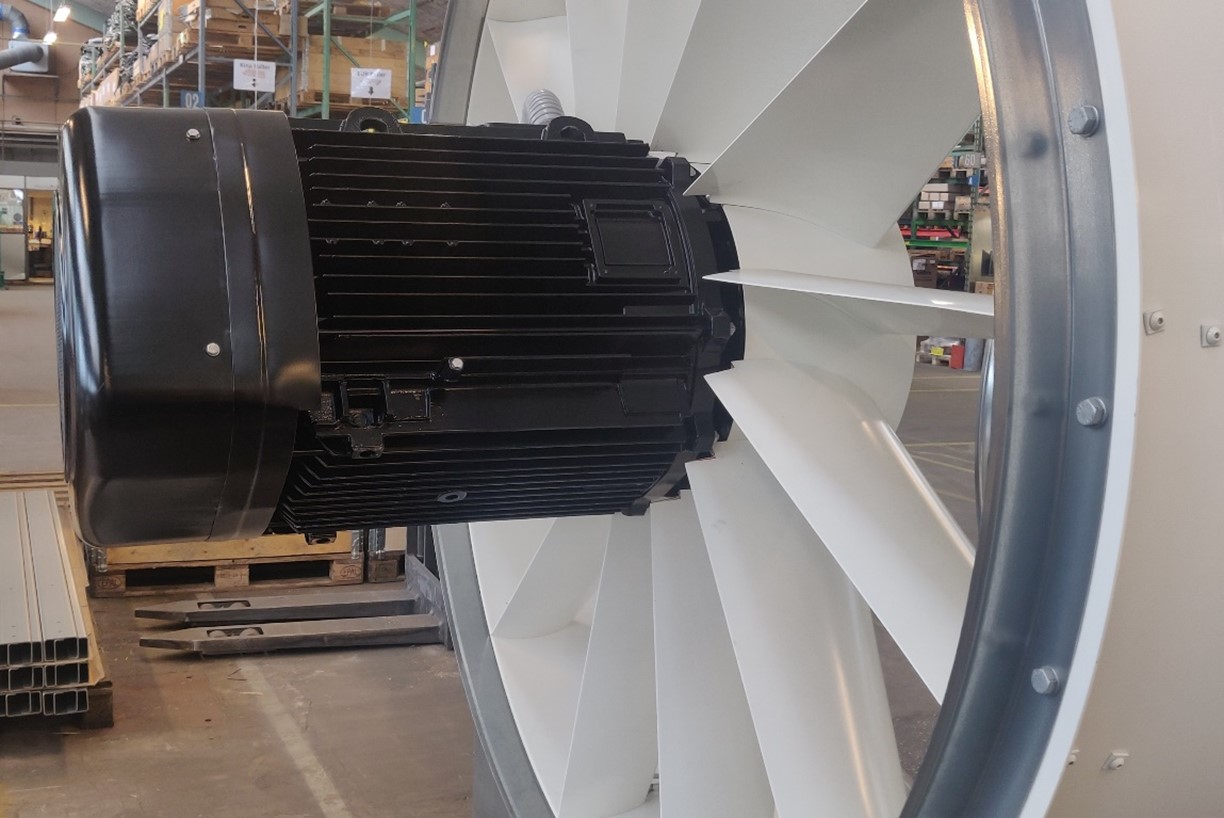
The site is the latest renovation project of the Teutschenthal backfill mine in Germany, operated by GTS (Grube Teutschenthal Sicherungs GmbH & Co. KG). Since the mining of potash and rock salt was stopped in 1982, the mine is used to store every year more than 200,000 tons of mineral waste materials produced by municipal and industrial plants. By using the cavities for the environmentally friendly and long-term safe disposal of mineral waste 700 meters below the surface, the backfill mine makes a significant and sustainable contribution to environmental protection. To improve ventilation systems under the ground intended for removing CO2 from stored mineral waste, a specially designed 36 m tall chimney was needed with a powerful air handling capability.
Implementing the Dyneo+ technology means less kWh consumed, fewer raw materials used and lower CO2 emissions, says Nidec. Compared with an IE3 induction motor, the frame size would be 315 mm and even 355 mm instead of 280 mm with the Dyneo+ motor. As for the weight, it would total 1300 kg in frame size 315, instead of 820 kg, thus half a ton lower, and the efficiency level of the motor powered by drive less than 96.5%. By combining an efficient extraction fan to the Dyneo+ energy-saving motor controlled by a frequency inverter, Novenco was able to provide an eco-friendly solution.
The Dyneo+ synchronous motors combine reluctance and permanent magnets, featuring a rugged mechanism using the same components as induction motors and rare earth-free rotor. They range from 11 to 500 kW and speeds up to 6000 rpm.
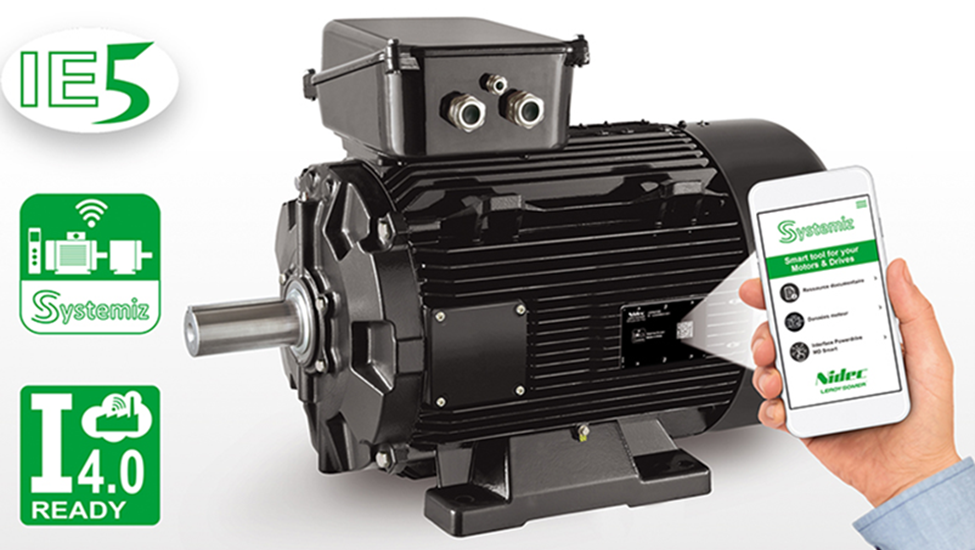
Combining the performance of synchronous permanent magnet technology and advanced smart system connectivity, they are drawing the attention of engineers conscious about energy efficiency for industrial applications. Designed for pairing with variable frequency drives, the motors meet the latest standards of leading governing bodies as they tighten restrictions on energy use.
Based on the mechanical platform of its IMfinity induction motors, the motors are built with a rotor free of rare-earth material, windings with reinforced insulation plus advanced digitization and sensing features. They are permanent magnet-assisted synchronous reluctance in design, incorporating all the benefits of induction and synchronous permanent magnet technologies including low rotor loss, the company notes.
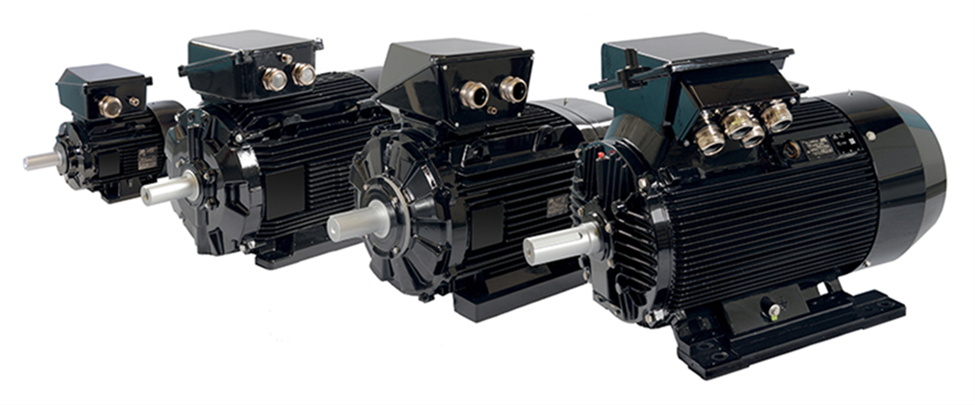
There are two variants. One version is interchangeable with a standard IEC motor, the other an extremely compact version to address space constraints and optimize energy consumption. Key applications include industrial refrigeration, compression, pumping, ventilation, extrusion, grinding and process industries. They provide an easy-to-implement solution for applications requiring high torque at high speed. High starting performance in sensorless mode avoids the need for an encoder. For more info, see www.nidec.com.