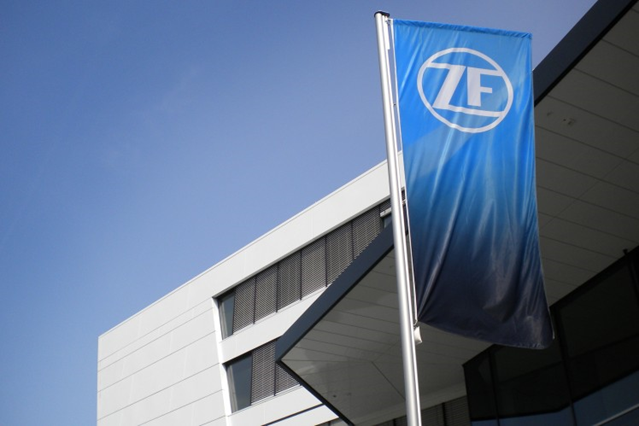
Looking like a standard bearer for top-tier automotive suppliers, ZF is slowly recovering from a staggering drop in business due to Covid-19 while steering a path toward greater use of magnets and magnetic technology as it retools to build more electric powertrains in the future. No more investment in technology exclusively for internal combustion engine powertrains, the company says, believing that the pandemic is actually accelerating the momentum toward e-mobility.
Based in Friedrichshafen, Germany, ZF reports that sales in the first half of this year fell 27% to €13.5 billion compared to €18.4 billion for the same period in 2019, resulting in a loss of €177 million.
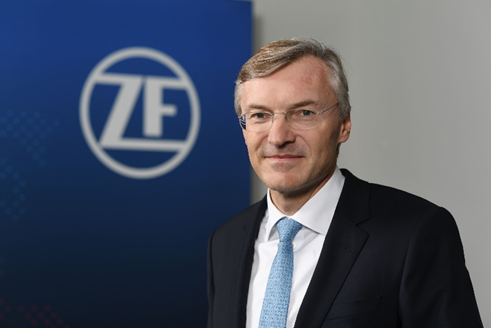
“Together with all ZF employees worldwide, we effectively adjusted our costs in March and reduced them by more than one billion euros in the first half of the year,” said CEO Wolf-Henning Scheider, addressing the figures for the first half of the year. “In the second half of the year we will now ramp up production everywhere, return to positive operational performance and realign structures and capacities for the long term.” He outlined measures to focus on adapting the company to the new economic and technological conditions, among them the establishment of a new division dedicated to electric vehicle powertrains as an important step in the company’s ongoing transformation towards e-mobility.
On January 1, 2021, a new division will be formed from the current Car Powertrain Technology and E-Mobility divisions to offer customers electrified driveline solutions from a single source. In the future, ZF will not invest in transmissions exclusively designed for internal combustion engine vehicles but will focus its development activities on flexible platform technologies for long-range plug-in hybrids and purely electric vehicles.
“The corona pandemic is noticeably accelerating the transformation of the automotive industry – we expect electrification to come even faster now,” said Scheider. The newly formed division will be able to leverage the system advantages of both divisions and offer vehicle manufacturers a comprehensive electrified drive portfolio as well as worldwide development and production capacities under one roof.”
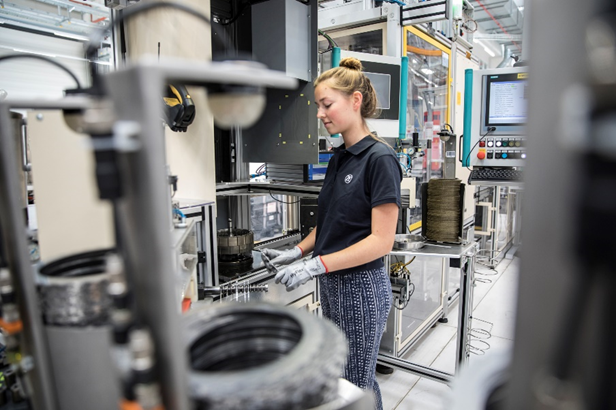
Beyond automobiles, ZF is also building its e-powertrain business in markets for buses, commercial vehicles and boats. Production was planned to start in the third quarter of this year on the company’s new CeTrax electric drive which has two electric motors close to the wheels. The power package with an output of up to 300 kilowatts and a maximum torque of 4,500 Newton meters is suitable for both buses and distribution trucks.
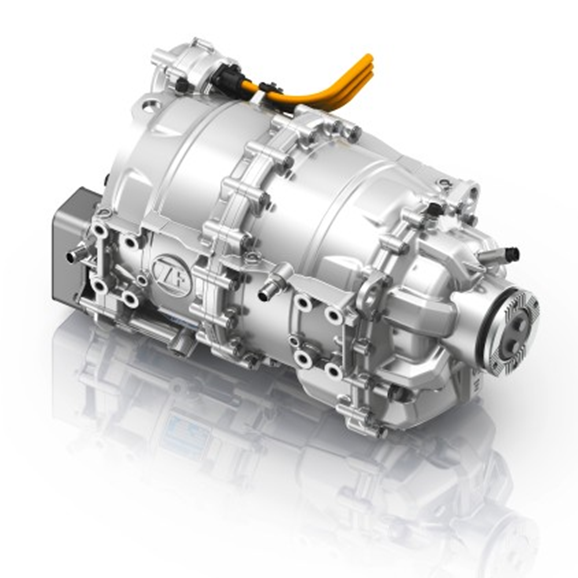
“With CeTrax, we are targeting manufacturers who want to integrate an electric drive into their existing classic bus models. Our CeTrax solution saves on costs and reduces the workload involved in technical integration as well as in service,” says Andreas Grossl, responsible for axle and transmission systems for buses and coaches at ZF.
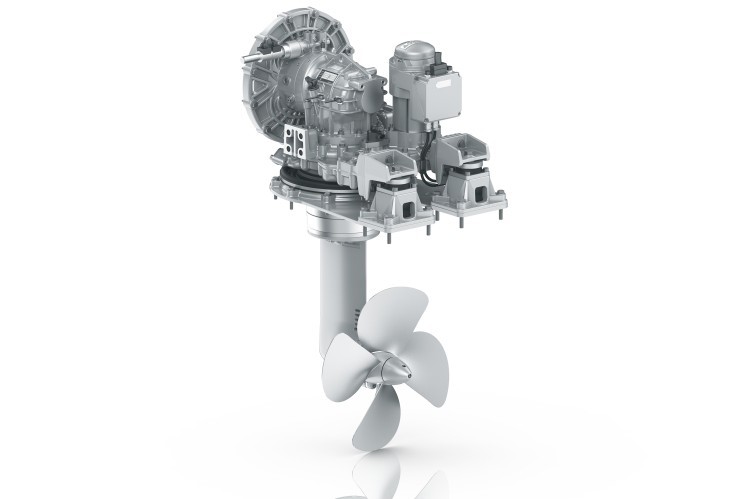
ZF is also developing a fully electric propulsion system for sailing yachts that uses an electric motor with a maximum output of 125 kW instead of the usual diesel unit. ZF is currently testing its electric propulsion system concept under real-life conditions, powering an innovation vessel equipped with the system that has been cruising Lake Garda in Italy since September 2019.
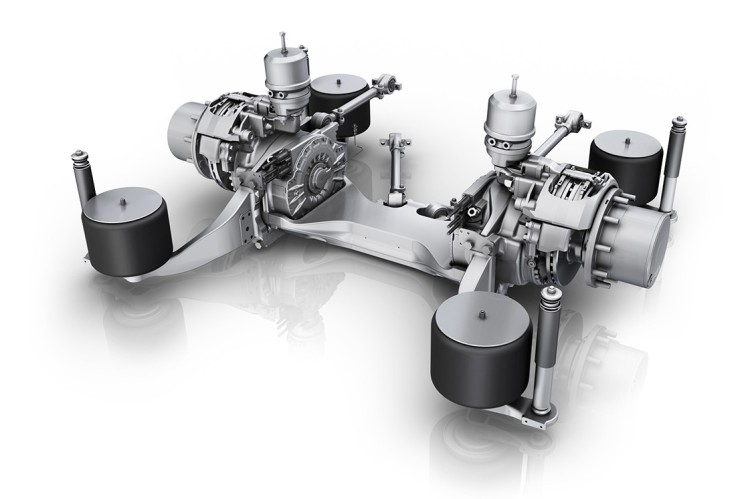
Designed for city buses, the company’s AxTrax AVE low-floor electric portal axle is powered by liquid-cooled electric motors that are integrated directly into the axle. The high-torque electric motors set fully loaded buses in motion quickly in urban stop-and-go traffic while offering emission-free driving.
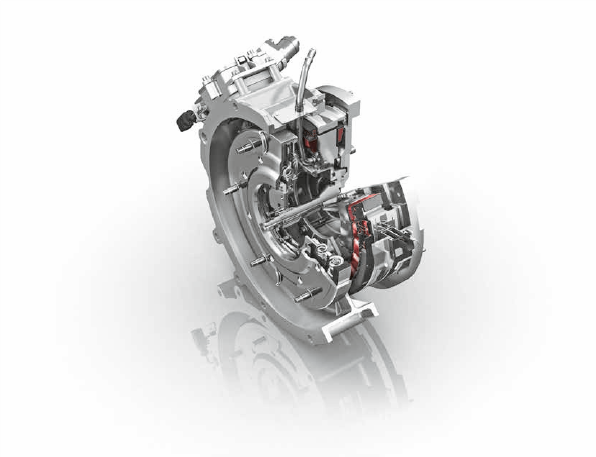
The DynaStart electric motor from ZF forms the basis for electrifying the driveline in many applications. Used in passenger cars, commercial vehicles and construction machines, the motor can be configured with internal or external rotor, depending on the needs of individual applications.
Dr. Matthias Beringer, a group leader in the Electric Traction Drives Business Unit whose team helps develop electric drives, especially at the start phase, commented on these fundamentals in a recent issue of ZF’s magazine, Vision. “For permanent magnet rotors in a synchronous motor, the material itself generates the necessary magnetism, thus ensuring a high level of efficiency. In contrast, for a rotor in an asynchronous motor, the magnetic field has to be generated by electricity. Which is better?
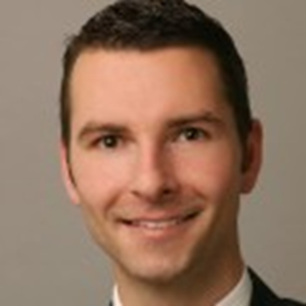
“These days, for passenger car applications, we usually prefer the 3-phase permanent magnet synchronous motors,” he noted. “However we are also able to rely on a broad technical portfolio of other machine topologies.”
“We are already extremely well set up for our next major project: 800 Volt electric motors which are becoming possible thanks to new power electronics (silicon carbide) and battery technologies,” he added.
ZF expects the market environment to remain very heterogeneous in the second half of the year. “Although Europe is showing signs of recovery at the moment, it will likely be the most critical region in the next few years due to declining vehicle exports and stricter emissions regulations,” said ZF CEO Scheider. Due to the high number of Covid-19 infections currently, development in the Americas is also very uncertain. “China and Asia are currently the most promising markets. Business in this region is coming back very strongly and is helping us to increase our sales again.”
Overall, the global economic situation remains tense, cautions Scheider. ZF does not expect the market to recover to 2019 levels in the next three years. “This applies to passenger cars and light commercial vehicles up to a weight of six tons, although our forecasts for passenger cars with 88.5 million units in 2023 are still far from the approximately 94 million units of 2018,” he explained. With heavy commercial vehicles, the upswing looks to be slower: in 2023, expected sales of 3.2 million heavy trucks will be 360,000 vehicles below the 2019 figure (3.56 million).
For more info, see www.zf.com.