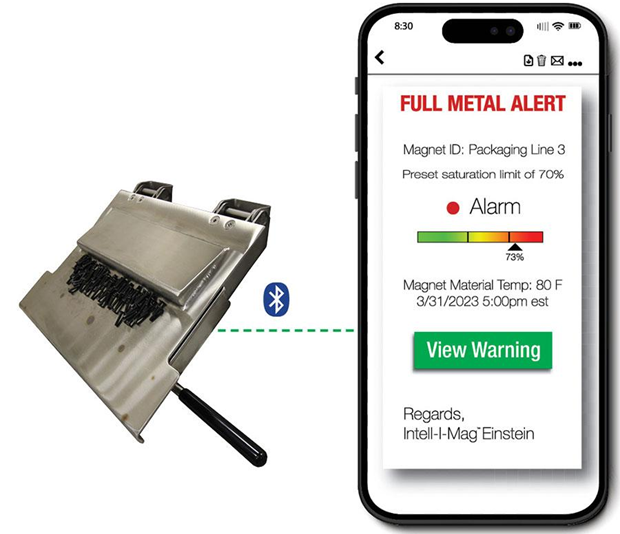
Knowing when the magnet in a magnetic separator needs to be cleaned – or, just as important, when it doesn’t – are very practical issues for users of magnetic separations equipment who want to safely maximize their uptime. Intelligence from the factory floor is valuable which is why Magnetic Products, a maker of industrial separations equipment, is enjoying a welcome reception to its new Intell-I-Mag system that applies smarts to the operation.
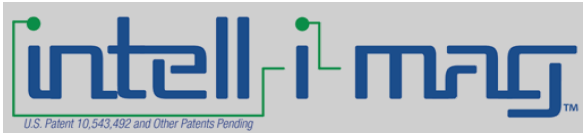
Basically, the company explains, traditional magnetic separation equipment has been “dumb”, operators have to shut down their equipment and check them at set intervals. Intell-I-Mag is the first magnetic separator that is “intelligent”. It tells you when the magnet needs to be cleaned, or, just as important, when it doesn’t. Key applications are in food manufacturing, metal forming and industrial processing. The system is available exclusively on its own equipment.
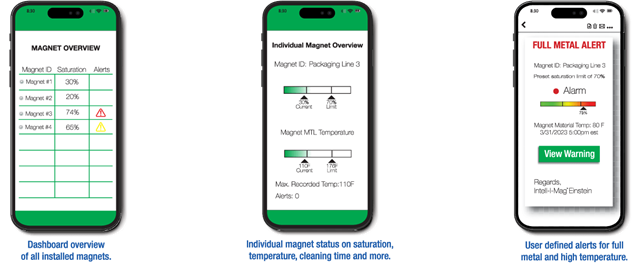
It was a fun, whirlwind tradeshow season in the the first half of this year as the MPI team traveled the U.S. to demonstrate the newly patented Intell-I-Mag, reports the company. This fall it will be ramping up the demonstrations again.
Its magnet experts have been presenting, How Intelligent Magnets Will Change the Way You Use Magnetic Separators, seen as particularly important in showing how Industry 4.0 technology will impact the way that magnetic separators have been used for decades. The Intell-I-Mag Einstein Monitoring Platform is a wireless cloud-based and Bluetooth monitoring system that enables operators to get real-time data from all their Intell-I-Mags on their cell phones or web browsers. With Intell-I-Mag everything happens in real-time.
The system monitors tramp metal saturation levels on the working surface of a magnetic separator. The magnetic separator has sensors embedded into the separator that measure the strength of the magnetic field. These sensors report data collected in real-time to a controller which can be programmed to alert operators when the separator reaches user defined saturation levels so they know when the magnet needs to be cleaned. It also monitors magnet temperature which can help avoid magnet degradation from overheating.
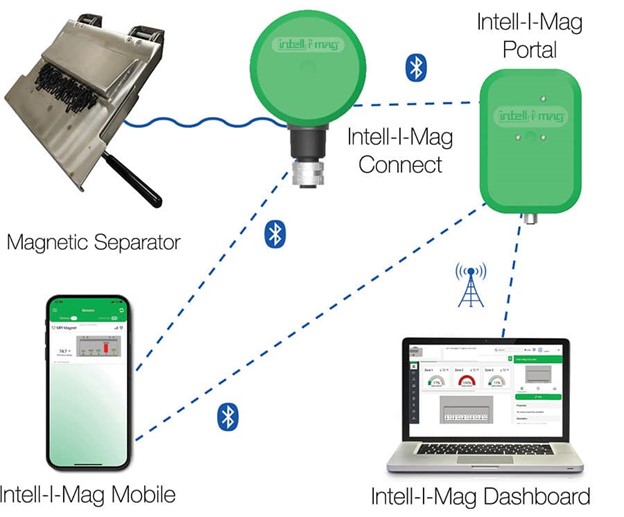
The Intell-I-Mag Local Monitoring Platform is a hardwired local monitoring system that enables operators to get real-time data from their Intell-I-Mag at a local controller installed in the facility. The controller can be configured to monitor, report and control single or multiple units. Users are able to integrate the control and data collection with plant operating systems or use it as a stand-alone system.
Operators can monitor an assortment of metrics and controls including magnetic separator saturation levels, data logging of system metrics and events, activate cleaning cycle (if automated), magnet position opened or closed (if automated with reed switches), cleaning cycle count, time since last cleaning, magnet material temperatures and maximum recorded magnet material temperature.
Based in Highland, Michigan, MPI specializes in magnetic separation equipment that removes ferrous contaminants from dry or liquid product flows. Its standard magnetic separators include gravity, pneumatic, liquid, and magnetic filtration equipment. It produces a large selection of metal sorting and magnetic conveyor systems, electronic inspection equipment, also automation and workholding products such as lifting magnets, magnetic chucks and sheet separators. For more info, see www.mpimagnet.com.