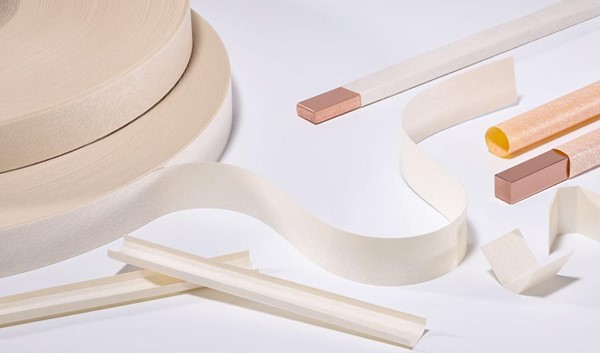
Engineers designing high-voltage motors and propulsion systems for today’s e-mobility markets must confront new challenges in thermal management. The more compact and more powerful motor systems with high power density generate intense heat over extended periods that can threaten performance. Care must be taken to optimize the service life of all motor components such as insulation, casting compounds, winding heads, magnet wire and magnets.
Krempel has developed a three-layer electrical insulation laminate, Trivoltherm E-Fluid-Safe, that can help. The latest generation of e-motors has higher voltages and thus a higher power density. This leads to increased waste heat due to mechanical friction and current-carrying conductors. Resulting in higher thermal loads for the components and materials. Conventional cooling methods such as air or water cooling reach their limits.
Thermal management based on direct contact cooling therefore is the future, says Krempel. The coolant flows directly through the engine and the heat is dissipated without diversion. Automatic transmission fluids are currently used as the coolant of choice in liquid-cooled motors. They offer good lubrication and electrical insulation with high thermal stability. Future developments will see them further optimized for direct cooling and marketed as so-called e-fluids.
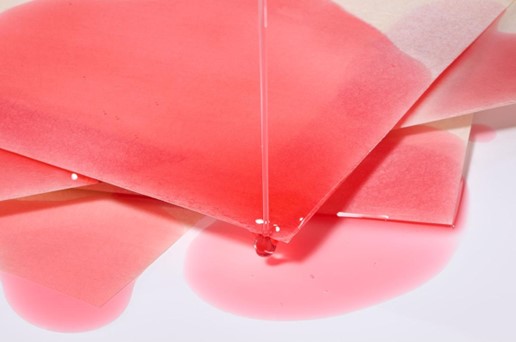
Trivoltherm E-Fluid-Safe was specially developed for use in directly cooled electric motors. The main applications are slot insulations, slot closures, stamped parts and intermediate insulations. It is provided in rolls and sheets for individual further processing in the manufacturing process or as individual stamped parts. It can also be produced in custom-fit small tubes with a range of diameters for hair-pin winding technology. See www.krempel.com.