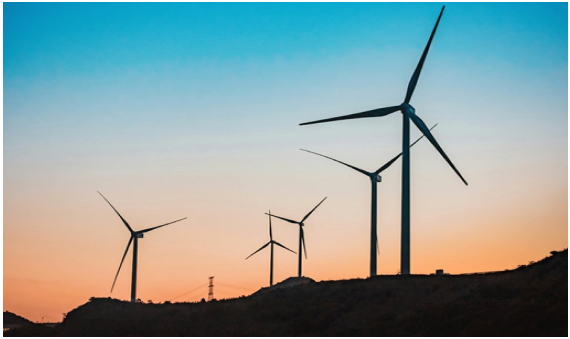
Cyclic Materials, a startup advanced metals recycling company in Canada intent on building a circular supply chain for rare earth elements (REEs) and other critical metals, has expanded its operations to accept two new feedstock streams: wind turbine generators and MRI machines. Through its growing partnership network, Cyclic has already sourced 37 MW capacity of wind turbine generators containing permanent magnets, and 116,000 pounds of MRI machines. The new development marks a strategic expansion for the company beyond automotive components and other permanent magnet-containing products into other end-of-life products.
Its proprietary Mag-Xtract and hydrometallurgy technologies are the first in the world with the capacity to isolate magnets from any end-of-life product and then convert this magnet feedstock to mixed rare earth oxides, cobalt-nickel hydroxides and other raw materials, says the company. Both wind turbine generators and MRI machines contain valuable materials such as neodymium, praseodymium, dysprosium, terbium and copper. While the recycling of metals such as aluminum, steel and copper in wind turbines is common, current recycling methods are unable to recover valuable REEs found in the generators, the largest of which can contain close to 10 metric tons of them, notably neodymium permanent magnets.

“MRIs and wind turbines bring incredible opportunities to recover critical commodities essential to the energy transition,” said Ahmad Ghahreman, CEO and co-founder of Cyclic. “Manufacturers, developers and stakeholders across metals supply chains must recognize the importance of creating a circular supply chain—not only to reduce dependence on offshore sources and increase resilience, but to slash the environmental impact of the industry. Our magnet-agnostic recycling technology extracts valuable critical metals from end-of-life products and feeds these commodities back into North American and European supply chains.”
Operating from its pilot facility in Kingston, Ontario which it launched in the fall of 2023, Cyclic is processing feedstock with a capacity of 8,000 metric tons per year. The company currently seeks additional sources for end-of-life wind turbine generators, MRI machines and other materials such as automotive parts and manufacturing waste. In the coming years, Cyclic is planning to expand with multiple facilities in North America and Europe, including a hub commercial demonstration facility to open this year with a magnet processing design capacity of 100 tons per year.
Founded in 2021, last year Cyclic closed an oversubscribed Series A Funding of $27M led by BMW iVentures and Energy Impact Partners, which followed a $3M funding from the Sustainable Development Technology Council of Canada. See www.cyclicmaterials.earth.