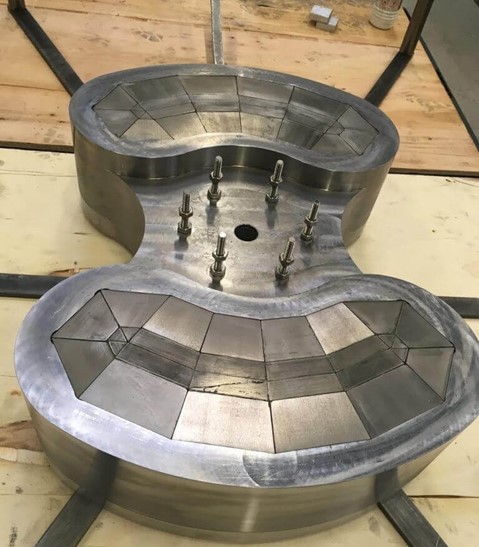
Supporting a Danish university research project in sustainable cooling, Bakker Magnetics has helped fabricate a magnetocaloric heat pump that involves one of the most complex magnetic systems it has ever built. Shown above are the two halves of the magnet system, as seen from below.
Magnetic cooling with water enables energy efficient cooling without the use of hydrofluorcarbon gases, a technique that the Technical University of Denmark (DTU) has been studying. The recent effort continues its well-established history of research in the field.
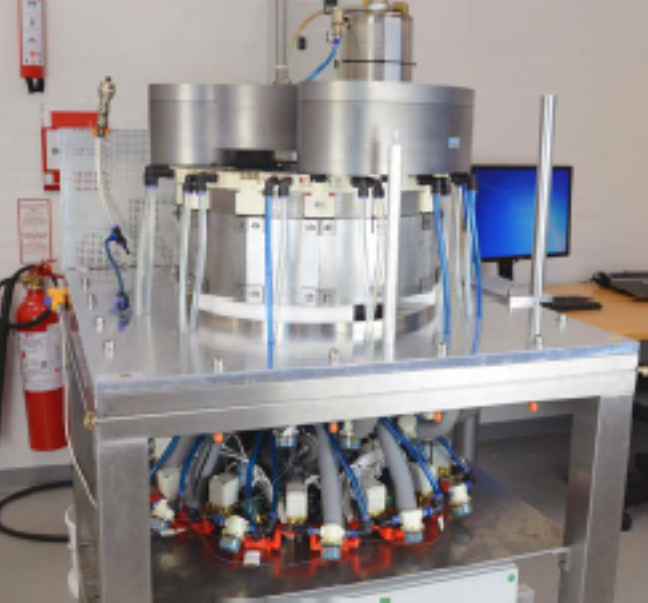
The magnetocaloric group at DTU designed a new prototype, called MagQueen. It is a magnetocaloric heat pump designed to supply the heating needs of a typical Danish house for one family. The project involved designing a rotary active magnetic regenerator heat pump device with a multi-bed concept.
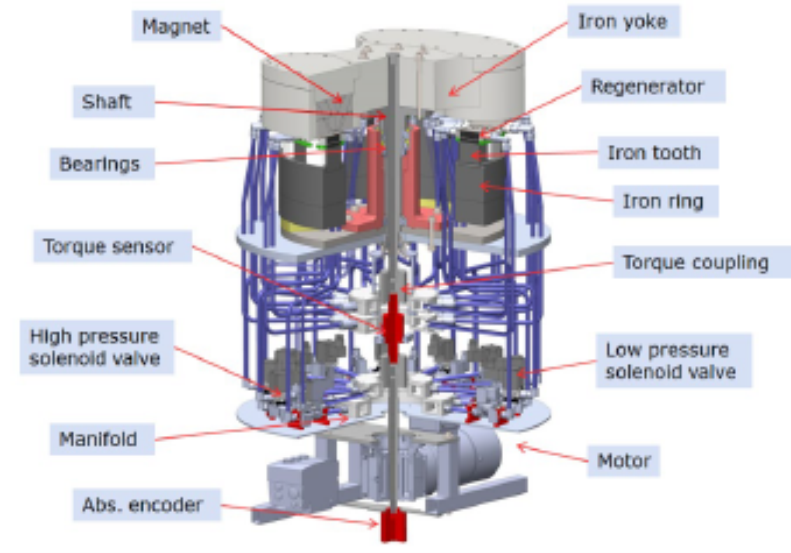
The innovation could potentially contribute to the goal of a CO2-neutral Europe. In addition to sustainable cooling, the versatile system can also provide space heating and hot water. Conceivable applications include refrigerators, wine coolers and air conditioners but this energy-efficient technology also has intriguing implications when it comes to cooling processes on a larger industrial scale.
Bakker’s part of the project has been to draw on its expertise to assemble the magnetic part of the pump and the magnetic forces involved, using highly complex Halbach arrays in the process.
A precise and accurate approach was key. One of the most complex systems that the company has ever built, it says, one of its employees spent six months assembling the magnetic component.
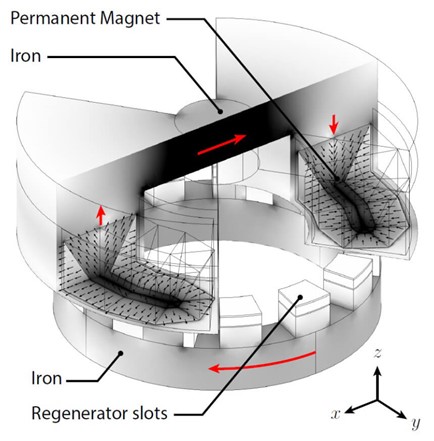
The design and experimental results of the device have been summarized by the team in a presentation on the project. Important design features are the rotating two-pole magnet assembly, the laminated iron ring, the 13 fixed tapered regenerator beds, and the dynamically adjustable parallel flow circuit. The optimized magnet design was developed with optimally shaped segments and optimum remanence for the desired magnetic field distribution. The magnetic system uses NdFeB permanent magnets producing an average flux density oscillating between 0 and 1.44 T in the air gap. The iron ring was laminated to reduce the eddy currents, allowing the device to run at cycle frequencies up to 3 Hz. The design of the regenerator housing was optimized with respect to parasitic losses and even flow distribution in both directions. The device produced a maximum heating power of 950 W, a performance that could be an important milestone in the development of future magnetocaloric devices, say the researchers.
Materials development is also a factor in such research as the magnetocaloric properties of certain metals are crucial. These properties operate in a limited critical temperature range and coming up with an alloy that offers a wide critical temperature range is a key aspect. Another company that collaborated on the project is Vacuumschmelze GmbH, a leading developer and producer of magnetic alloys.
According to Bakker, its collaboration with the university stems from a long-standing relationship based on its years of experience and knowledge of magnetism, materials, adhesive properties, coatings and the dangers involved in working with magnetism. Headquartered in Eindhoven, The Netherlands, the company also cooperates with other universities in the field of applied magnetism including University of Salerno, University of Ljubljana and Federal University of Santa Catarina in Brazil. For more info, see www.bakkermagnetics.com, and www.dtu.dk.