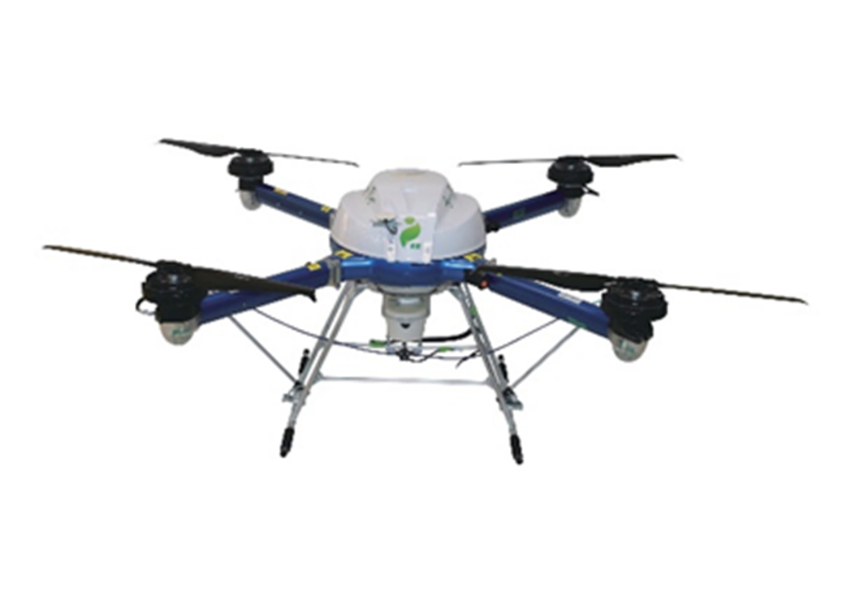
Using advanced injection molded magnet assembly and special coil winding technology, Aichi Steel and Sawafuji Electric have partnered in the development of a new motor for industrial drones that weighs 30% less than conventional models.
They have begun supplying the motors to drone manufacturers and are planning to move into mass production. The motors use injection-molded bonded magnets made of Aichi Steel’s dysprosium-free Magfine material, and aluminum wire windings.

While drones are an anticipated countermeasure against worsening labor shortages in fields such as distribution and farming, weight reduction remains a pressing issue to support increased carrying capacity and flight time. The new motor offers some compelling advantages for improved drone capability, say the partners. It has been tested in both a full-electric drone (shown at top) and a hybrid drone.
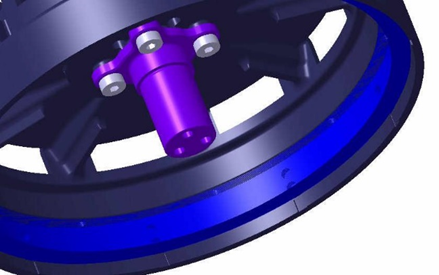
Aichi Steel says that it has developed new magnet assembly technology that uses injection molding resulting in increased motor output and weight reduction from molding a large bore multipole magnet into a magnesium housing. The combination of high magnetic force, positioning freedom and high dimensional accuracy succeeded in achieving the reduced weight and contribute to longer flight times for drones.
Vibration is reduced also. By optimizing the direction of the magnetic field during magnet molding, pulsating torque during rotation, a source of vibration, can be reduced by approximately 20%, realizing stable attitude control by the drone.
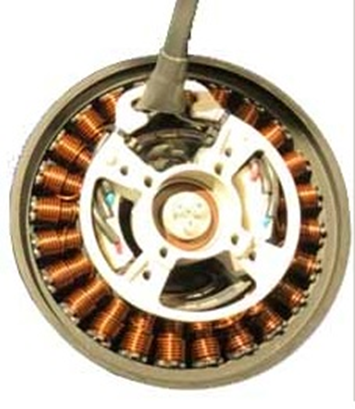
The coil winding uses aluminum wire rather than copper, relying on winding technology with a proven track record in generators and other products. This allows for a long-lasting, lightweight motor with stable insulation performance, say the partners.
Future plans call for the companies to leverage their new motor development efforts in order to expand applications into motors that require more complex shapes, Steps envisioned include improving the performance of the magnetic powder which is used as a base material as well as further development of injection molding and winding technology.
Detailed test results including charts and diagrams are available at www.aichi-steel.co.jp.