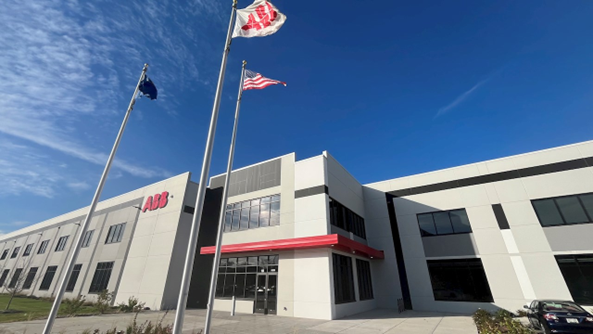
ABB has begun the phased opening of a new $100 million campus in Wisconsin to increase production capacity of industrial electric drives in the U.S., its largest market. Likely, the facility and its eventual 700 staff will also stimulate growth in North America of its new magnet-free industrial motors that can be coupled with the company’s drives for energy efficiency, along with continued placement of drives with direct torque control technology for controlling flux and torque in motors. The highly automated production facility will be complemented by a digital Customer Experience Center and a state-of-the-art Innovation Lab, also a warehouse distribution center, all packaged with numerous eco-friendly facility enhancements.
“ABB is a technology leader in electrification and automation and the U.S. market is an important growth engine for our business,” said Brandon Spencer, President of ABB’s Motion Business Area. “Investment in this modern manufacturing facility gives ABB access to a highly qualified workforce, strengthens localized supply chains, and keeps us close to our customers.”
“ABB is strengthening America’s infrastructure and introducing new, cleaner technologies to help customers boost competitiveness while lowering their carbon footprint,” said Tuomo Hoysniemi, President of ABB’s U.S. Motion Business Area and Global Drive Products Division. Kelly Kling is Drives Site Leader for the facility, and Head of Finance for US ABB Motion Business.
ABB has a world-class extensive lineup of drives and motors for industrial applications. While the specific drives to be produced at the new plant were not announced, below are a few examples of current products that could be coming together there.
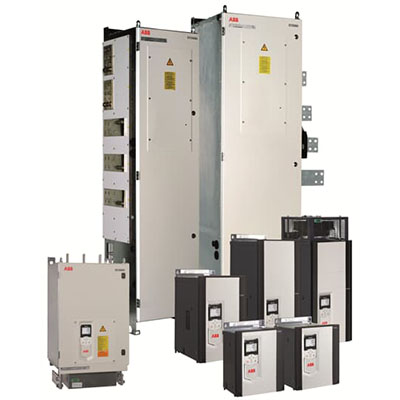
ABB’s new DCS880 DC drive series is built on the all-compatible drive platform that ensures all variable speed drives from the company share common features and tools, and can be operated in the same way. There is a wide range of options to serve any DC motor application, they are also suitable for non-motor applications like magnets, battery charging, electrolysis and wastewater treatment.
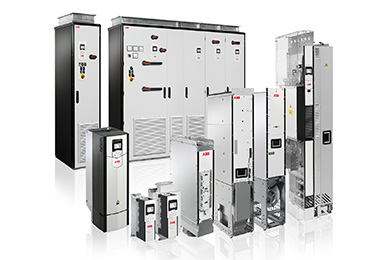
Built-in Direct Torque Control (DTC) is a key feature of ACS880 industrial drives, suitable for many applications including the chemical industry. They are designed to run reliably even in non-ideal supply network conditions including voltage fluctuations. The technology ensures high starting torque of the motor resulting in highly reliable process start.
DTC is an optimized AC drives control principle where inverter switching directly controls the motor variables: flux and torque. The measured input values to the control are motor current and voltage. The voltage is defined from the DC-bus voltage and inverter switch positions. The voltage and current signals are inputs to an accurate motor model which produces an exact actual value of stator flux and torque every 25 microseconds. Stator flux is a measure of the magnetic strength in the stator windings of a motor, caused by a current running through a coil.
Motor torque and flux two-level comparators compare the actual values to the reference values produced by torque and flux reference controllers. The outputs from these two-level controllers, updated every 25 microseconds, indicate whether the torque or flux has to be varied. Depending on the outputs, the switching logic directly determines the optimum inverter switch positions. The result is that every single voltage pulse is determined separately at “atomic level”. The inverter switch positions again determine the motor voltage and current, which in turn influence the motor torque and flux and the control loop is closed.
Variable-speed drives have enabled unprecedented performance in electric motors and delivered dramatic energy savings by matching motor speed and torque to the driven load requirements. Most VSDs in the market rely on a modulator stage that conditions voltage and frequency inputs to the motor, but causes inherent time delay in processing control signals. In contrast, premium ABB drives employ DTC, significantly increasing motor torque response.
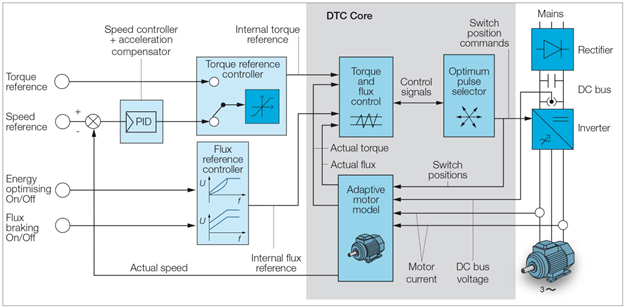
Originated by one of the founding companies of ABB and patented in the mid-1980s, DTC eliminates the need for an extra modulator stage thus achieving control dynamics close to the theoretical maximum.
When ABB introduced its first direct torque control AC drive to the market in 1995, DTC was already a leading technology. Subsequent improvements in processor computational power, application programming, and communication interfaces have continually enabled higher DTC performance for a broad range of applications.
Drives coupled with magnet-free motors for increased energy efficiency

Lately, ABB has increasingly been matching some of its drives with new SynRM magnet-free motors for achieving new levels of energy efficiency. The push began with a version that met IE5 standards for motor efficiency and recently the company has launched a next-generation IE6 Hyper-Efficiency version that targets meeting expected future IE6 standards. The synchronous reluctance motors are designed to combine the performance of a permanent-magnet motor with the simplicity and service-friendliness of an induction motor. The rotor in a SynRM motor has neither magnets nor windings and suffers virtually no power losses. The design also requires no rare earth metals and offers a high level of usability due to the wide availability of suitable variable speed drives for control.